What is O ring
o-ring is a loop of elastomer with a round (o-shaped) cross-section used as a mechanical seal or gasket. They are designed to be seated in a groove and compressed during assembly between two or more parts, creating a seal at the interface. (wikipedia.com)
O-Rings are torus-shaped (i.e. doughnut-shaped) objects made from elastomeric compounds such as natural or synthetic rubber, and are used to seal mechanical parts against fluid movement (air or liquid). O-Rings perform their sealing action by deforming to take the shape of their cavity, after being oversized to guarantee an predetermined interference fit.( efunda.com)
O ring typically used in one of two seal designs, axial or radial, in mold design to attaching cavity to mold base axial, face type are commonly used then radial type, because axial type is more easy to assembly in mold than radial type.
2D O ring drawing like picture below
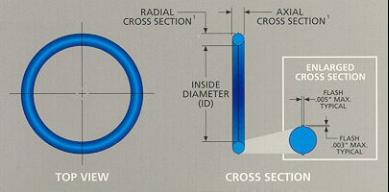
Static seals exist where there is no relative motion between the mating surfaces being sealed.
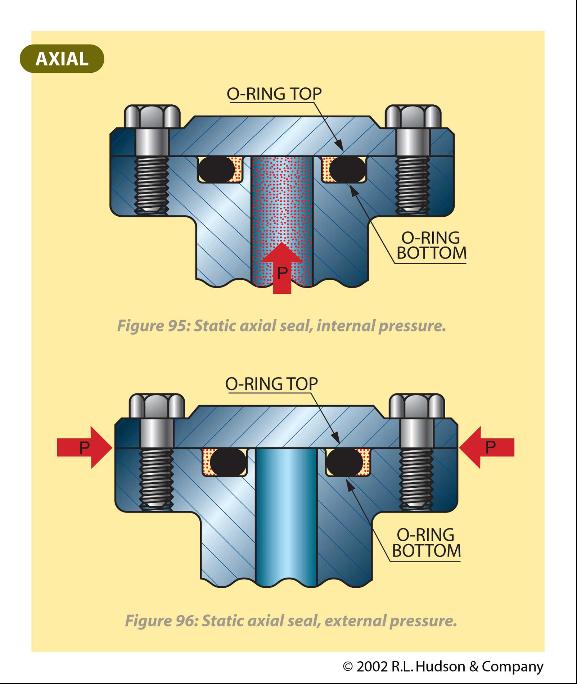
at previous post about basic construction for joining cooling system in cavity and mold base , we can learn how to joint pipe from mold base of mold to cavity site.
various construction can be develop from basic construction, previous post basic construction is fast and cheap construction model, but it isn't good when you in large mold and mass production mold, why? becouse production mold must have endurance until 1000 000 shot.
Picture below shown develop construction of joining cooling pipe
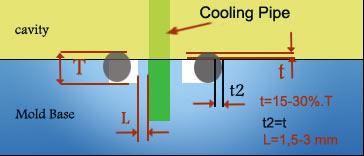
blue color indicate mold base side and yellow color indicate cavity side.
basic rule from those picture are :
1. T is height of O ring
2. part of O ring that will receive pressure form cavity plate. 15-30% from it's height is best. this little pressure give to prevent leak when water flow in cooling system.
3. t2 value is same with t, but t2 is horizontal, becouse O ring always made from elastomer plastic, by little pressure we can add O ring to O ring hole.
4. L is Gap between cooling channel and O ring hole.
O-Ring Design Considerations
1. Proper Squeeze
•Compression expressed as a percentage of the free-state cross-sectional thickness:

•Face Seal: 20-30%
•Static Male/Female: 18-25%
•Reciprocating: 10-20%
•Rotary: 0-10%
2. In static seals, where the O-Ring is not in axial motion in the bore, the recommended maximum compression is approximately 40%.
3. The O-Ring must be compressed by a predetermined amount, and this compression determines the O-Ring cross-section diameter.
4. The O-Ring inner diameter is typically chosen to be close to the groove's inner diameter; by selecting it to be slightly less than the groove's inner diameter, the O-Ring will stretch and hug the groove.
5. The Groove Width must be larger than the O-Ring cross-section diameter, to accommodate the radial expansion of the O-Ring when it's axially compressed in the gland.
6. stretch,
- Excessive stretch can overstress material, thin cross section, and reduces % squeeze
- % cross section reduction due to stretch about half of the % ID stretch
7. Sharp Corners, make R in cornet to prevent damage during seal installation.
8. Pressure and Clearance Gap.
Most elastomeric seals are designed to operate within ambient pressure to about 1,500 psi. At very high pressures, the seal must have sufficient strength to resist extrusion into the clearance gap. The chart at right illustrates the recommended limits of the combination of clearance gap (diametral), seal hardness, and pressure differential. picture below shown graph between clearance gap and pressure
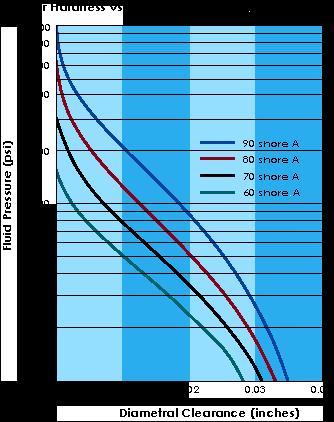
9. When it is said that an elastomer is good for an application it is meant that some compounds which include that material are acceptable. Not All. For instance, some compounds of EP are good for brake fluid applications, but most are not acceptable.
10. DO NOT use a lubricant composed of the same material as the O-ring. For example, a silicone lubricant should NOT be used with a silicone O-ring.
11. Avoid using graphite-loaded compounds with stainless steel, as they tend to pit the stainless steel surface over time.